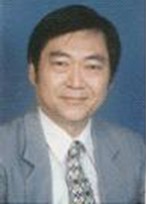
陶樹令 老師
- 所在地區(qū): 不限地區(qū)
- 主打行業(yè): 不限行業(yè)
- 擅長領(lǐng)域:生產(chǎn)管理
- 企業(yè)培訓(xùn)請(qǐng)聯(lián)系董老師
- 聯(lián)系手機(jī):

陶樹令老師培訓(xùn)聯(lián)系微信

掃一掃,關(guān)注公眾號(hào)
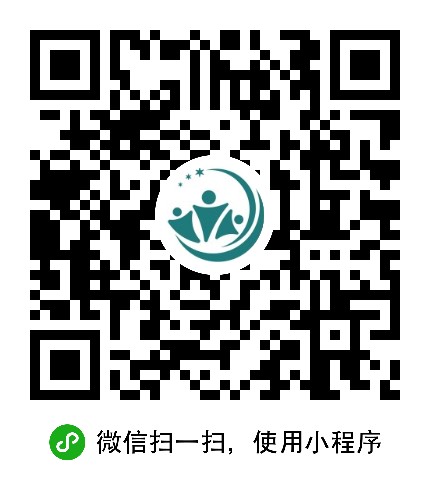
陶樹令老師的內(nèi)訓(xùn)課程
部份:企業(yè)流程再造(BPR)的運(yùn)作一、何謂顧客二、企業(yè)面對(duì)3C的挑戰(zhàn):三、企業(yè)再造四、再造企業(yè)的重心五、四個(gè)方面的企業(yè)再造六、企業(yè)再造的原則七、企業(yè)再造成功的關(guān)鍵因素八、流程再造的前提和條件九、為達(dá)成目標(biāo),企業(yè)采用的方法十、企業(yè)改造工程的關(guān)鍵精神十一、改進(jìn)成效比較圖十二、企業(yè)再造的實(shí)施步驟十三、管理變革下的七種反彈:十四、外在環(huán)境的變化:十五、組織經(jīng)營管理上的挑戰(zhàn):十六、重新思考討論流程:十七、流程再造之作法:十八、流程再造的特色十九、新融合式的經(jīng)營管理第二部份:生產(chǎn)流程設(shè)計(jì)一、什么是流程二、何謂流程管理三、TQA的架構(gòu)(制造業(yè))四、導(dǎo)入流程管理的四個(gè)階段五、 流程管理的成功要領(lǐng)六、流程及表單
講師:陶樹令查看詳情
一.品質(zhì)的發(fā)展二.品質(zhì)的定義三. TQM的定義四.全面品質(zhì)經(jīng)營管理(TQM)的必要性五. TQM的六大基本觀念(Concepts)六.何謂顧客(作業(yè)一):內(nèi)部顧客的改善七.全面品質(zhì)經(jīng)營管理的真諦(作業(yè)二):持續(xù)改善轉(zhuǎn)弱為強(qiáng)八. TQM在文化上的改變九.日常管理及方針管理十. TQM系統(tǒng)的基礎(chǔ)A)整合PDCA循環(huán)(SDCA及OVPA)(作業(yè)三):PDCA改善循環(huán)B)進(jìn)展及改善的階段十一.推進(jìn)TQM的關(guān)鍵成功的因素(作業(yè)四):TQM的手法(作業(yè)五):如何改善員工的意識(shí)型態(tài)(作業(yè)六):統(tǒng)合綜效十二.企業(yè)面對(duì)3C的挑戰(zhàn)十三.學(xué)習(xí)曲線十四.透過過程處理創(chuàng)造價(jià)值(作業(yè)七):共同利益方(作業(yè)八):員工素養(yǎng)的
講師:陶樹令查看詳情
前半段(3.5小時(shí))1、IE技術(shù)基礎(chǔ)◆IE的原理與發(fā)展歷史◆IE技術(shù)的核心內(nèi)容和追求目標(biāo)◆工廠如何活用IE思想◆訓(xùn)練員工用IE的眼光看問題2、生產(chǎn)力與生產(chǎn)效率的衡量指標(biāo)◆生產(chǎn)效率與企業(yè)競(jìng)爭力◆效率評(píng)價(jià)指標(biāo)3、效率改善的基礎(chǔ)與改善方向◆運(yùn)用IE技術(shù)改善的原理、原則◆消除瓶頸◆現(xiàn)場(chǎng)7種浪費(fèi)分析◆如何減少浪費(fèi),保持流程增值◆如何快速切換,提高系統(tǒng)效率4、制造程序分析與改善◆ 流程程序圖分析◆加工效率的改善◆檢查效率的改善◆停滯與等待的分析與改善5、動(dòng)作效率分析與改善◆動(dòng)作分析的要領(lǐng)◆動(dòng)作活性指數(shù)介紹◆運(yùn)用動(dòng)作分析提高動(dòng)作效率◆運(yùn)用動(dòng)作經(jīng)濟(jì)原理提高效率6、作業(yè)效率分析與改善◆人機(jī)作業(yè)分析◆人機(jī)配合效率
講師:陶樹令查看詳情
一、前言lTPM之緣起及發(fā)展過程lTP的定義lTPM的基本理念lTPM的目標(biāo)lTPM的必要性lTPM的定位二、生產(chǎn)活動(dòng)之失誤及損失 2.1各部門之作業(yè)失誤2.2設(shè)備六大損失三、TPM的步 3.1 TPM與TQC之特色 3.2 TPM與TQC、5S之關(guān)系四、零故障之出發(fā)點(diǎn) 4.1零故障之五大對(duì)策五、TPM之設(shè)備診斷技術(shù)六、TPM之效果測(cè)定與評(píng)價(jià) 6.1 TPM之效果測(cè)定之定義 6.2 TPM效果測(cè)定之方法 6.3 TPM之效果測(cè)定與評(píng)價(jià)七、TPM之推展 7.1導(dǎo)入TPM之12步驟7.2 TPM的推行機(jī)構(gòu) 7.3小集團(tuán)活動(dòng)的基礎(chǔ)知識(shí) 7.4各種小集團(tuán)活動(dòng)的推行要領(lǐng)八、TPM的新展開
講師:陶樹令查看詳情
1.概論2.生產(chǎn)管理和生產(chǎn)管制2.1生產(chǎn)管理2.2生產(chǎn)管制2.2.1生產(chǎn)管制的功能和組織2.2.2生產(chǎn)形態(tài)簡介2.2.3生產(chǎn)管制制度之建立2.2.4生產(chǎn)計(jì)劃2.2.5工時(shí)分析2.2.6產(chǎn)能分析2.2.7生產(chǎn)排程【日程計(jì)劃】2.2.8進(jìn)度跟催2.2.9異常處理2.2.10生產(chǎn)績效分析3.多種少量訂單生產(chǎn)方式的特點(diǎn)3.1訂單形態(tài)3.2管制方式3.3物料管理4.多種少量訂單式生產(chǎn)體制的建立4.1目標(biāo)4.2應(yīng)有的認(rèn)識(shí)(觀念)5.多種少量訂單式生產(chǎn)管理的重點(diǎn)5.1業(yè)務(wù)5.2生管/物管5.3制造現(xiàn)場(chǎng)5.4工程開發(fā)5.5管理者應(yīng)俱備的能力6.排程研究6.1制造業(yè)的排程問題6.1.1制造業(yè)的排程問題6.1.2
講師:陶樹令查看詳情
1.前言1.1人—工作—成果之關(guān)系1.2管理之本質(zhì)2.何謂PAC績效管理制度2.1績效分析與控制2.2 1956年日本能率學(xué)會(huì)“門田武士”所創(chuàng)2.3績效管理乃『時(shí)間管理』之一種3.績效與生產(chǎn)力之關(guān)系3.1附加價(jià)值為中心之經(jīng)營3.2勞動(dòng)生產(chǎn)力3.3生產(chǎn)力的改善著眼點(diǎn)4.損失工時(shí)與績效4.1工時(shí)之結(jié)構(gòu)4.2日本企業(yè)損失工時(shí)之責(zé)任區(qū)分統(tǒng)計(jì)4.3造成損失工時(shí)之原因4.4作業(yè)績效之表示5.PAC績效管理之特征5.1依科學(xué)的標(biāo)準(zhǔn)時(shí)間來評(píng)價(jià)作業(yè)績效5.2可強(qiáng)化線基層干部之指導(dǎo)力5.3工時(shí)損失之責(zé)任可明確區(qū)分5.4績效的分析報(bào)告與控制5.5適當(dāng)配置機(jī)動(dòng)單位元5.6作為獎(jiǎng)工制度之基石6.PAC制度之設(shè)立6.1績